3) Critical Speed
The critical speed can be
calculated by the following equation:
1st Mode RF x 60
1st Mode Critical Speed = ----------------------- (rpm)
Number of Blade
2nd Mode RF x 60
2nd Mode Critical Speed = ------------------------ (rpm)
Number of Blade
For example, fan diameter
= 28 ft and number of blade = 9,
1st mode critical speed =
6.3 x 60 / 9 = 42.0 rpm.
(1st mode RF of 28 ft - 9 = 6.3 hz)
(Note that the 2nd mode RF
do not need to consider.)
4)
Resonant Frequency Margins
A first resonant peak ideally
should not occur between "0" hz and the fans
operating speed. If one does occur during acceleration
from rest, it will show up only as a momentary "shudder",
since most of fans reach full speed within 3 seconds
or less. In case of variable speed drive however, a
resonant peak between "0" and the operating
speed presents a real problem. The fan must be prevented
from running steady state at or near the resonance speed
by means of an electronic lock-out of a narrow speed
range.
In most cases, there is not
necessary to consider the first critical speed and only
to carefully consider the second critical speed. Typically,
we recommend minimum 5% of RF separation between the
first mode RF frequency and the blade passing frequency,
or between the first mode RF frequency and the beam
passing frequency. In any cases, beam passing and blade
passing frequencies could not occur within the + 5%
to - 5% of any RF modes. This is most important requirement
in sizing a fan. (Note that the beam passing frequency
consideration is not required for the steel or wood
structure having the narrow beams.)
(1) RF Margin with Blade
Passing Freq.: The formulations must be differently
applied to obtain the RF Margin per the value in difference
of first mode RF and blade passing frequency as follows;
Case I : First Mode RF >
= Blade Passing Frequency
First Mode RF - Blade Passing Freq.
RF margin = ------------------------------------------------
x 100 (%)
First Mode RF
Case II : Blade Passing Frequency
>= First Mode RF
Blade Passing Freq. - First Mode RF
RF margin = -------------------------------------------------
x 100 (%)
First Mode RF
(2) RF Margin with Beam Passing
Freq.
Case III : First Mode RF
> = Beam Passing Frequency
First Mode RF - Beam Passing Freq.
RF margin = -------------------------------------------------
x 100 (%)
First Mode RF
Case IV : Beam Passing Frequency
>= First Mode RF
Beam Passing Freq. - First Mode RF
RF margin = -------------------------------------------------
x 100 (%)
First Mode RF
(3) Adjustment of RF Margin:
The first mode RF is a fixed value as per the fan size
& no. of blade. Only a choice for deciding this
margin depends on the factor of blade passing frequency.
For increasing the RF margin
it is required up or down the blade passing frequency
with the adjustment of fan speed or number of fan blades.
In case that the first mode RF is smaller than the blade
passing frequency. (Case II), it is necessary to increase
the blade passing frequency. This is very simple.
In opposite case that the
first mode RF is larger than the blade passing frequency
(Case I), in order to reduce the blade passing frequency
it is required to decrease the fan speed or to decrease
the number of fan blades. Lowering the number of blades
or decreasing the fan speed, it could be another problem,
which might exceed the maximum brake horse power per
blade or which might be a considerable increase of brake
horsepower of fan due to less number of blade.
Normally, we recommend that
the fan bhp per blade must lower than the maximum bhp
per blade by 4 bhp, since the fan blade of fiberglass
composite may be damaged due to over torque. Especially
if you did not consider the wind velocity surrounding
the cooling tower at the initial fan design, it is necessary
to have more margin for the maximum bhp/blade since
fan bhp per blade might exceed considerably the maximum
bhp/blade due to increase of airflow volume and static
pressure due to wind velocity.
There is still a problem
to decrease the number of blade. In reducing the fan
rpm the fan pitch will be increased and the fan bhp
will increase, too. Therefore, the problem is still
same as reducing number of blades. So, you are required
to increase the fan diameter.
Meantime, it is not simple
to control the beam passing frequency since number of
supporting beam is almost fixed and could not be adjusted.
Only a choice is to increase or decrease the fan speed
with the gear reducer.
For increasing the RF margin
it is required up or down the beam passing frequency
with the adjustment of fan speed. In case that the first
mode RF is smaller than the beam passing freq., (Case
IV), it is necessary to increase the fan speed in order
to increase the blade passing frequency.
In opposite case that the
first mode RF is larger than the beam passing freq.
(Case III), in order to reduce the beam passing frequency
it is required to decrease the fan speed. In case of
decreasing the fan speed, it could be another problem
as mentioned previously.
(4) Blade Harmonic Constants:
The potential for magnification of forces when a critical
range (resonance) is zero is very great, and depends
on definition of harmonic constants and damping factors.
The harmonic constant (KH) is a factor that
is a function of wavefront conditions: it describes
the potential of a blade to resonate in the harmonic
situation (N = 2, 3, 4, ...) relative to an N = 1 first
order response. The amplification factor (AF) of the
blade can be calculated by: AF = KH + {[1
- (N x rpm/fd)2]2 +
[2 z x (N x rpm/fd)]2}1/2,
where the damping factor z
= ln [x/(x + 1)] and x is the amplitude. At resonance,
the frequency ratio N x rpm/fd equals 1,
and the magnification factor (MF) by substitution into
the above equation is: MF = KH/2 z.
Damping factors typically
range from about 0.012 for metal blades to 0.036 for
foam filled fiberglass polyester blades. The harmonic
constants have been estimated to range from 0.24 to
1.0. Critical range and potential of the system should
be investigated at fan installations where breakdowns
are consistent or occur early in operating life. If
it is determined that the system is approaching a critical
range of operation, several remedies are possible. The
easiest solution may be to disrupt the air-impulse excitation
frequencies through removal or rearrangement of obstructions
in the plenum. This will lower the harmonic constant
of the tower, but can never remove all amplification
potential.
A more positive method is
to change the dynamic natural frequency of fan and move
it out of critical range. This can be done either by
changing the speed of the fan or by weighting the blades
to change the natural frequency. In most cases, weighting
the blades proves to be the more economical solution
to the problem.
(5) Relation with Cooling
Tower Structure and Blade Passing Frequency: In a cooling
tower, air is moving over obstruction or beams blocked
inlets, etc. It could mean a possible interaction in
the structure or fan stack with blade passing frequency.
Note that Hudson does not cover the frequency interaction
in a cooling tower structure besides supporting beams
since they are beyond fan maker's control. This interaction
between the operating frequency and tower itself (i.e.
blade passing frequency interaction with fan stack natural
frequency) could be suited by tower manufacturer to
avoid the resonant problem at tower.
In the application of wood
structure tower and FRP fan stack, a special attention
is required. To avoid the running of fan in the tower
structure resonance and to control the vibration with
the 80 microns at the gear reducer or the motor frame,
the number of blades have to be carefully selected.
For your information, 6 mils (1 mil = 0.001" =
25.4m, peak to peak) is the
maximum vibration allowed on Air Cooled Heat Exchangers
specifications. So, Hudson has adopted API spec. of
6 mils for gear reducers on cooling tower structures.
It has been realistic for US constructed wooden towers.
This is to be considered
a maximum limit on the gear reducer itself not a normal
level. Common practice in US is to use the minimum recommended
number of blades to reduce the vibration in the wood
structure tower and FRP fan stack. This is to avoid
dangerous air load induced pulsation on the fan cylinder.
The fewer blades are occurring the higher air loads
and are enlarging the more intense blade passing pulsation.
If you ask to guarantee the
levels as low as 3 mils (0.003" = 76.2 microns),
the dynamic field balancing would be required for the
fans. Of course, the number of blades must be increased
from the minimum number of blades (described in
Chapter
1
) at 80 microns or less requirement of vibration.
To achieve the vibration limit on the wood structure
tower and FRP fan stack, a check of frequencies must
be done that there are no tower resonance at the blade
passing frequency or 1 x fan rpm 60 frequency. While
the concrete tower are so structurally stiff. So, fan
vibration is rarely a problem.
If a vibration problem occurs
in the field there are several options to correct the
problem: First, you have to analyze the amplitude versa
frequency for positively determining the problem. You
are required to plot them via a vibration analyzer.
This shows immediately amount of vibration and its frequency
which tells where the vibration occurs. If the vibration
occurs at the fan blade passing frequencies, the tower
structures is in resonance with the fan blade passing
frequency. This is not a problem of fan balance. It
is very difficult to stiffen a wooden structure of fan
stack. Most of time, to increase the number of blade
is the least costly solution. But, if the problem was
occurring at 1 x fan rpm / 60 (hz), this problem is
due to the unbalance of fan assembly, which must be
corrected properly by fan maker.
Meantime, you can easily
understand that the fan stack is in resonance with fan
blade passing frequency if you remove the fan stack
(if the materials of fan stack is made of FRP) and run
the fans at the rated rpm. Unless the problem is in
1 x fan rpm / 60 (hz), it's not a problem of fan balance.
[If you consider the total unbalance as a vector (weight
at some distance), it moves out of the plane of rotation
only one time per revolution. Hence, 1 x fan rpm / 60
(hz) equals fan unbalance.] In general, the unbalance
of fan could be corrected per below actions.
- Minimize tip track variation
which is a major source of dynamic imbalance.
- Check the proper assembly
of fan including hardware tightness, blades in the
proper position, and blades at the equal pitch.
- Balance the fan "in
place"
(Note: "In place" balancing is effective
because it takes the mass of the existing machinery
mount and dynamic imbalance into consideration.)
- Change the fan blades
or entire fan.
5) Fan Vibration Monitoring
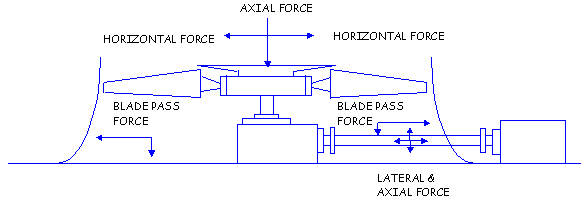
A cooling tower fan is a
rotating machine subject to the same laws of physics
as any other. Cooling tower fans have three qualities
that make dealing with them a special challenge. These
qualities are 1) wet and corrosive environment, 2) slow
rotational speeds, and 3) a wide range of support structure
rigidity.
The basic fundamentals of
vibrations are 1) All machines vibrate. 2) Vibration
is caused by forces generated by rotation, reciprocation
and impacts. 3)Vibration frequency equals rotational
or reciprocating speed and multiples or repetition rate
of impacts. 4) Many machine faults produce vibratory
forces as follows;
- Unbalance at one time
RPM.
- Aerodynamic unbalance
at number of blades times RPM
- Misalignment at one, two
and three times RPM
- Looseness at two times
RPM
- Gear Faults at number
of teeth times RPM
- Faulty rolling element
bearings at RPM multiples
It is not the vibration that
is harmful. Vibration is the symptom of the presence
of vibratory forces and the mechanical faults that cause
them. Forces cause wear and destruction not vibration.
This view of vibration is most important when related
to rotating machinery maintenance. From this viewpoint
there are no vibration problems. There are mechanical
problems that reveal their presence by the way they
cause the machine to vibrate. Correct the mechanical
problem and the symptom, vibration, will go away.
A typical cooling tower fan
arrangement consisting of drive motor, drive shaft,
gear reducer, and the fan. The fan normally rotates
slowly, is multi bladed, with high tip speeds. The support
structure may be wood, concrete or steel and not as
stiff as the designer would like because of compromises
made in favor of unrestricted air flow. The environment
is usually highly corrosive and wet. This means most
materials will deteriorate in time, producing a variety
of problems.
|