In the late 1970's the energy crisis reached a peak.
In the years since the oil crisis, many industries who
utilize electric power, such as refinery and petrochemical
have started to study for the energy saving. The field
of cooling tower was not excepting. To minimize investment
cost and realize improved cooling tower operational
economy (with minimal loss to production) the designer
should evaluate the effect of cooling tower size and
performance on plant output. To do this, the impact
of the design point on tower size and the effect that
the many possible modes of tower operation have on cold
water temperature must be more completely understood.
With today's trend towards
minimum energy use firmly established, it is necessary
for cooling tower users to continuously reassess both
the operational requirements and the design point parameters
given to potential equipment suppliers. This is quite
essential to insure the most economical tower operation
over the life of the system.
1) Cooling Tower Thermal
Design Strategy
Several parameters are used
to develop the tower design. These are water flow rate,
cooling range, and wet-bulb temperature. Of these only
the wet-bulb temperature is not process related and
therefore affords us some flexibility. Determining the
impact the design wet-bulb temperature has on the size
and power requirements of a cooling tower is critical
to optimizing the cooling tower economics. For this
reason, an example illustrating this effect will be
discussed further.
In the majority of applications,
the design duty of an evaporative cooling tower is based
upon an acceptable/required cold water return temperature,
when operating under constant heat load, and local wet-bulb
temperature conditions. If investment and operational
costs were not a concern, the ideal design wet-bulb
temperature would be equal to, or higher than, the highest
local wet-bulb temperature recorded. In this way, the
returned water temperature would never be higher than
the acceptable/required cold water temperature.
Unfortunately, this design
methodology can lead to large, power intensive cooling
towers which are rather expensive. Instead, the design
wet-bulb temperature chosen is usually a compromise
between operational requirements and capital cost. In
order to reduce the tower's size, or power requirements,
and therefore the cost of the tower, the specifier normally
chooses a wet-bulb temperature which is not expected
to be exceeded for more than a small percentage of the
time in any given year. in effect, the actual wet-bulb
temperature used for design then, is lower than the
ideal wet-bulb temperature. The acceptable/required
cold water temperature returned by the tower will be
achieved at this new lower design wet-bulb temperature.
A value of 2.5 or even 5%
of the total yearly operating hours is normally the
amount of time acceptable/required cold water temperature
is permitted to be exceeded. Actually, the value used
should depend upon the process, and the effect cold
water temperature have on the process. in some cases,
values of 1-1/2 or even 1% are used.
Below figure is a typical
wet-bulb temperature cumulative frequency diagram. it
has the classic "5" shape and with it we can
determine what percent of the year the cooling tower
can be expected to experience a particular wet-bulb
temperature. For this case, it can be seen that the
design wet-bulb temperature would be exceeded 0.5 percent
of the year, i.e., about 58 hours. For such a tower
the plan area would be about 4,608 square feet (this
size, of course, is dependent upon the manufacturer's
design, fill and fill air velocity). In this example,
we will assume that the fill, fill air velocity, water
flow rate and cooling ranges are kept constant.
The percentage of time the
ideal wet-bulb temperature can be exceeded. As a general
rule, as the percentage of time exceeding the ideal
wet-bulb temperature is increased, the plan area of
the tower decrease. Thus the total evaluated cost (i.e.,
initial investment plus operational costs) to the user
is decreased. However, it must be pointed out that since
the tower's cooling capacity is reduced, the plant's
output is also correspondingly reduced. If taken to
the extreme this will have severe production impact.
Conversely, as the number of hours is reduced, the tower
size and power requirements increases. Obviously, so
does the investment and operational costs, but the yearly
production of the plant also increases. (This is the
basis for an optimization process, since as the percentage
of time increases, the average yearly production of
the plant will decrease.)
Inlet (hot) water temperature:
113oF (45oC)
Outlet (cold) water temperature: 89.6o (32oC)
Wet-bulb temperature: 82.4o (27oC)
Water flow rate: 63,842 GPM (14,500 M3/hr)
Tower Size: 42' x 42' x 6 cells
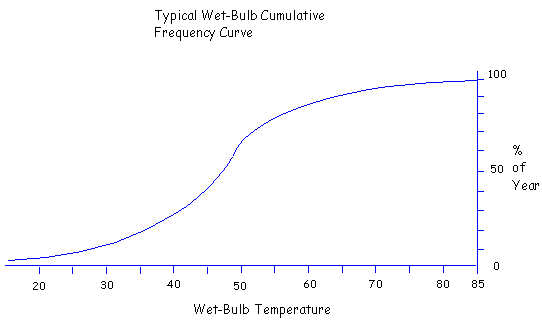
Clearly, then, when choosing
the design point the specifier must be cognizant of
the effect the cooling tower design point has on plant
operation. The design point should be chosen such that
it yields a cooling tower which provides the minimum
cooling capacity which does not produce a severe adverse
effect upon plant performance. Thus, the careful consideration
of the design parameters is essential as a basis for
cooling tower operating economy and operating efficiency.
2) Component Design
Till now the economy was
discussed for only the thermal design side of cooling
tower. Let me discuss on energy evaluation for mechanical
counter flow type of cooling tower further. Fans, cylinders,
drift eliminators, fill and water/air distribution systems
are the components most subjected to the punishment
of the cooling tower environment and are therefore the
most commonly replaced. Since a cooling tower is an
air and water management device, those components which
are subject to the maximum wear and tear fortunately
also afford the greatest potential for improvement by
applying state of the art technology. For the fans and
cylinders were previously discussed. So, these shall
not be described in this section.
(1) Fill: Counter flow tower
design and operating experience has been accumulated
for over 60 years. The earliest and most common designs
until recently utilized splash type fills. The advent
of high power evaluations, beginning in the mid-1970's,
led to a predominance of film type counter flow designs
using relatively low cost PVC materials. The new film
type designs provide energy savings both in fan power
and pump head through the high surface areas per cubic
feet of fill. This "surface density" coupled
with its low cost gives film type counter flow fill
an overall effectiveness such that it has become an
industry standard.
The component most likely
to provide improvement in tower performance is the fill
packing. In some cases, merely replacing the filling
“in kind” can be the most cost-effective approach. If
the fill is in poor condition, bringing the tower back
to its original performance has an immediate, beneficial
impact on the operation of the plant. In most cases,
however, the owner should look at the high performance
splash and film fills that are available today. High
performance plastic fills, when properly installed,
offer the opportunity of improving the performance of
tower while at the same time providing a material that
is generally impervious to rot and chemical attack.
At typical cooling tower
thermal duties, the capacity of a given tower can usually
be improved several percent by replacing wood lath fills
with modern, high performance splash designs. Care must
be exercised when replacing fills. Any new fill will
likely have a pressure drop characteristic different
from the original equipment. The system designer and
tower owner must be aware of this and analyze the impact
a pressure drop change may have on the system as a whole.
High density splash fill is very efficient thermally;
but at constant horsepower, the air rate through the
tower reduces due to an increase in static pressure.
Normally the increased thermal efficiency more than
compensates for the reduction in air rate, but the fan
system must be checked to assure that it is capable
of moving the required air volume through the fill section
without stalling. A fan operating in a stall condition
is noisy, will not operate efficiency, and will not
move the required amount of air through the fill.
Conversely, some low pressure
drop splash fills, such as those that operate parallel
to airflow, must be investigated to assure that drift
problems do not occur. Due to the splash bar orientation
with respect to the tower air stream, less turbulence
is generated, reducing the thermal efficiency of the
packing. This effect needs to be overcome by increased
airflow through the tower. Fortunately, the reduction
in turbulence and in the projected area of the splash
bar reduces the operating pressure drop. At constant
horsepower, the resulting increase in airflow normally
compensates for the reduction in efficiency. The additional
airflow required, however, may increase the tower drift
rate. The designer must be aware of this and assure
that upgrading the fill performance does not generate
an objectionable drift rate.
PVC films are much more thermally
efficient than splash fills due to the tremendous water
surface that they expose to the air stream. As with
the high density film fills impose high pressure losses
on the air moving system. Additionally, film fills must
be provided with very precise water distribution to
assure full thermal performance. Unlike splash fills,
which tend to allow water redistribution and are somewhat
forgiving to marginal distribution systems, film fill
does not allow redistribution and is intolerant of poor
initial distribution. It is obvious that circulating
water cannot migrate across or through film fill sheets,
and research shows very little tendency for water to
migrate parallel to the fill sheets. Note that the small
stream of water applied at the top of the pack has expanded
only slightly by the time it reaches the bottom of the
fill. The practical implication of this is that unless
the circulating water is uniformly distributed over
the entire fill plan area, actual performance levels
may be much less than anticipated by the owner or fill
maker.
While film fill is extremely
efficient thermally, extreme care must be taken in its
application. Film fill is much more sensitive to fouling
than splash fill, and for this reason, is normally not
applied in systems where heat exchanger leaks, suspended
solids or biological conditions in the circulating water
indicate fouling potential. The purchaser and fill manufacturer
must communicate early in the fill selection process
to confirm water conditions and clogging potentials.
(2) Drift Eliminators: The
design o drift eliminators has undergone tremendous
improvement in the last decade. Concern about the discharge
of cooling tower drift has prompted new eliminator designs
that now routinely achieve elimination rates several
orders of magnitude lower than those available only
10 years ago. Some new eliminator configurations accomplish
this improvement while actually reducing eliminator
pressure losses - affording the owner an additional
opportunity to achieve operating horsepower savings.
The basic concept of eliminator
design is rather simple. A cooling tower drift eliminator
is a low pressure, momentum filter. Components are arranged
to force the air leaving the fill section to make a
series of directional changes. Water droplets, which
cannot negotiate these turns, impinge on the surface
of the eliminator, from which they are collected and
drained back into the wet side of the tower. The designer's
goal is to provide the maximum drift elimination at
reasonable cost and minimum pressure loss.
The state of the art in eliminator
design is the modern cellular configuration. Cellular
eliminators are typically constructed of PVC sheets
vacuum formed into very precise, compound shapes, with
an integral honeycomb strength. The compound shape allows
significant improvements in drift eliminations and the
use of cellular structure appreciably reduces the pressure
losses through the eliminator when compared to either
the wood lath or wave form eliminators. The net free
are of well-designed, modern cellular eliminators is
in excess of 95%.
As with all other tower components,
the design of the drift eliminator has an impact on
the rest of the system. Very subtle changes in the drift
eliminator can have a significant impact on the fan
system. For instance, the last "pass" in the
drift eliminator must direct the air upward toward the
fan. If this step is not taken or is taken improperly,
increased fan plenum losses will occur which could reduce
tower performance by as much as 10%.
(3) Water Distribution: The
distribution of water to the top of counter flow fill
is a key aspect of assured performance. It is a function
of nozzle design, nozzle installation pattern, spray
chamber height, and the structural cleanliness of the
spray chamber. The impact of water distribution on performance
is a combination of uniformity of water distribution,
air-side pressure drop through the spray chamber, and
heat transfer occurring in the spray zone.
The challenge for a spray
system designer is to accomplish an optimum balance
of design parameters with practical considerations such
as resistance to silt build-up, and the ability to pass
objects from trash to Amertap balls.
To provide the primary function
of precise water distribution, the nozzle must be designed
with other considerations in mind:
- ● The location of counter
flow nozzles and the potential for poor quality circulating
water demands that the nozzle system be designed to
minimize fouling. While small diameter, high pressure
nozzles or nozzles with internal turbulators simplify
the distribution function, they also greatly increase
the risk of fouling which increases the owner's maintenance
costs. Minimum clearance inside an industrial counter
flow nozzle should be at least 1-1/4" to avoid
the risk of plugging.
- ● The nozzle must be capable
of proving uniform distribution over a wide range
of flows, without significant loss in nozzle performance.
- ● The nozzle must be capable
of efficient operation while consuming a minimum of
expensive pump energy.
To be continued.
Please press the next button....
|