Now that we have examined the thermal side and cooling
system of cooling tower economy. Energy consumption
in mechanical draft cooling towers is confined to the
fan and pumps. Minimizing annual energy consumption
in the fan drive equipment is achieved not only by proper
specifications, but also by prudent operation.
- ● Cooling water bypass (manual)
- ● On-off fan operation (manual)
- ● Louvers or shutters (automatic)
- ● High efficiency motors
- ● Two-speed fan speed (manual
or automatic)
- ● Variable speed fans (automatic)
- ● Variable pitch fans (automatic)
The several major different
methods to drive the fans shall be discussed hereto.
The oldest and simplest is probably the cooling water
bypass method. This is merely bypassing the thruput
if the cooling water is overcooling. On-off fan control
is simple and is often used if there are a large number
of fans in an identical service. Automatic louvers are
the first step to modulated air flow. The only problem
is that the fan horse-power is wasted as the flow is
throttled by the louver. At complete shut-off the fan
is stalled and horsepower actually increases. The details
for the other methods are described in below.
1) Efficiency Motor
Using a high efficient motor
is a simplest way to be able to reduce energy consumption.
The motors called "High Efficiency", "Energy
Saving Motor", or "Premium Energy Efficient
Motors" were introduced in the late 1970's. The
technology and manufacturing changes during that time
were allowed to increase and ongoing the efficiencies.
Figure graphically depicts
a 89% efficient 175 HP motor coupled to a fan load requiring
175 HP (130 KW) of mechanical input power. The total
electric input power is 146.7 KW of which 146.7 KW is
converted to mechanical power required by the fan load.
This motor actually consumes 16.7 KW of power in the
process converting the electrical energy to the mechanical
energy to do useful work.
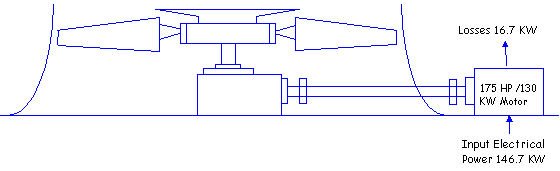
The emphasis on motor efficiency
and the energy conservation potential has spawned new
lines of "Energy Efficient" motors. These
premium efficiency motors offer substantial reduction
in motor losses and, when applied, can reduce the industrial
power consumption significantly. In most cases, the
motor's initial price premium can be totally justified
in energy savings and, in many cases using total life
cycle costing considerations, the entire motor cost,
not just the initial price premium, can be justified.
Useful cost justification
methods associated with the application of the energy
efficient motors shall be discussed below for users
of electric motors.
(1) Efficiency: Motor efficiency
is a measure of the effectiveness with which a motor
converts electrical energy to mechanical energy. It
is defined as the ratio of power output to power input
or, in terms of electrical power, watts output to watts
input and can be restated as the ratio of output to
output + losses. The difference-watts loss - is due
to electrical losses plus friction and windage. Even
though higher horsepower motors are typically more efficient,
their losses are significant and should not be ignored.
In fact, higher horsepower motors offer the greatest
savings potential for the least analysis effort, since
just one motor can save more energy than several smaller
motors.
(2) Watts Loss: Every AC
motor has five components of watts losses which are
the reasons for its inefficiency. Watts losses are converted
into heat which is dissipated by the motor frame aided
by internal or external fans. Stator and rotor I2r
losses are caused by current flowing through the motor
winding and are proportional to the current squared
times the winding resistance (I2r). Iron
losses are mainly confined to the laminated core of
the stator and rotor and can be reduced by utilizing
steels with low core loss characteristics found in high
grade silicon steel. Friction and windage loss is due
to all sources of friction and air movement in the motor
and may be appreciable in large high-speed or totally
enclosed fan-cooled motors. The stray load loss is due
mainly to high frequency flux pulsations caused by design
and manufacturing variations.
(3) Improvements of Watts
Losses: Improvements in motor efficiency can be achieved
without compromising motor performance - at higher cost
- within the limits of existing design and manufacturing
technology.
Watts
Loss Area |
Efficiency
Improvement |
1.
Iron |
Use
of thinner gauge, lower loss core steel reduces
eddy current losses. Longer core adds more steel
to the design, which reduces losses due to lower
operating flux densities. |
2.
Stator I2R |
Use
of more copper and larger conductors increases
cross sectional area of stator windings. This
lowers resistance (R) of the windings and reduces
losses due to current flow (I) |
3.
Rotor I2R |
Use
of larger rotor conductors bars increases size
of cross section, lowering conductor resistance
(R) and losses due to current flow (I) |
4.
Friction & Windage |
Use
of low loss fan design reduces losses due to air
movement. |
5.
Stray Load Loss |
Use
of optimized design and strict quality control
procedures minimizes stray load losses. |
(4) Evaluating Motor Efficiency:
Today's motor user faces the evaluation of higher efficiency
motors at premium prices with standard designs. In many
applications, an initial purchase price premium can
be justified based on energy cost savings. The basis
for this justification depends on the individual user's
situation. Factors such as running hours, cost of electricity,
payback period, cost of capital and service life affect
the premium price justifications, and will vary with
the individual user.
There are two methods for
user determination as to how much additional capital
investment or price premium is justified per kilowatt
of power load reduction. If, for example, an additional
capital investment of $1,000/KW is determined, the motor
user would be justified in paying up to a $1,000 price
premium for every KW saved because of the watts loss
reduction by using a more efficient motor. An example
of the power or watts loss reduction provided by a higher
efficiency 175 HP motor follows:
- ● Watts Losses = Input -
Output = (HP x 0.746 / Motor Efficiency) - (HP x 0.746)
- ● Watts Losses with 89%
efficiency motor = (175 x 0.746 / 0.89) - (175 x 0.746)
= 16.135 KW
- ● Watts Losses with 95%
premium efficiency motor = (175 x 0.746 / 0.95) -
(175 x 0.746) = 6.871 KW
Operating the 95% efficiency
motor vs. the 89% efficiency motor thus saves 9.264
KW. In other words, the power loss reduction is 9.264
Kilowatts. Kilowatt saved can be calculated using a
simple formula below.
Kilowatts Saved = HP x 0.746
[ (1 / Standard Motor Efficiency) - (1 / Premium Motor
Efficiency) ]
The method of calculating
the additional capital investment to justify the price
premium per KW of loss reduction are shown next:
- ● Simple Payback: The first
method is a simple payback analysis where the user
specifies how long he is willing to wait for his after
tax power cost savings to equal the premium paid.
The user must specify: P = Justified price premium/KW
saved = HRS/YR x $/KWH x YRS x (1-T)
Where,
HRS/YR: hours of motor operation per year
$/KWH: Cost of electricity (dollars or Korean Won
per kilowatt hour)
YRS: Maximum acceptable years to payback or break
even
T: Tax rate
A motor user that averages three - 8 hour shifts per
day; 6 days a week; 50 weeks per year has a power
cost of $0.46/KWH and considers two years breakdown
or payback period and has a tax rate of 22.5%.
Then,
P = HRS/YR x $/KWH x YRS x (1-T)
= (8 x 3 x 6 x 50) x $0.46 x 2 x (1 - 0.225) = $5,133.60
This user could justify up to a $5,133.60 price premium
for a motor that saved or reduced the KW load by 1
KW. Using the two alternative efficiencies in the
previous 175 HP motor example, this user could justify
paying an initial price premium for the high efficiency
motor of up to $47,557.7. (P x loss reduction = $5,133.60
x 9.264 KW = $47,557.67)
There are three basic components of industrial power
cost: cost of Real Power used; power factor penalties
and demand charges. To understand these three charges
and how they are determined, a review of the power
vector diagram identifies each component of electrical
energy and its corresponding energy charge.
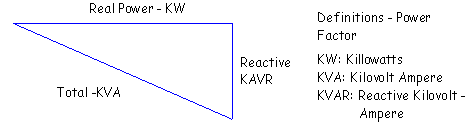
- ● Real Power: The Real Power-KW
is the energy consumed by the load. Real Power-KW
is measured by a watthour meter and is billed at a
given rate ($/KWH). It is the Real Power component
that performs the useful work and which is affected
by motor efficiency.
- ● Power Factor: Power factor
is the ratio of Real Power-KW to Total KVA. Total
KVA is the vector sum of the Real Power and reactive
KVAR. Reactive power is required to support the magnetic
field of the induction motor. Although Reactive KVAR
performs no actual work, an electric utility must
maintain an electrical distribution systems, (i.e.
power transformers, transmission lines, etc.) to accommodate
this additional electrical energy. To recoup this
cost burden, utilities may pass this cost on to industrial
customers in the form of a power factor penalty, for
power factor below a certain value.
Power factors in industrial plants are usually low
due to the inductive or reactive nature of induction
motors, transformers, lighting and certain other industrial
process equipment. Low power factor is costly, and
requires an electric utility to transmit more total
KVA than would be required with an improved power
factor. Low power factor also reduces the amount of
Real Powerthat a plant's electrical distribution system
can handle, and increased line currents will increase
losses in a plant's distribution system.
A method to improve power factor, that is typically
expensive, is to use a unity or leading power factor
synchronous motor or generator in the power system.
A less expensive method is to connect properly sized
capacitors with induction motors provides lower first
cost and reduced maintenance expense. Below figure
graphically shows how to the total KVA vector approaches
the size of Real Power vector as Reactive KAVR is
reduced by corrective capacitors. Because of Power
Factor correction, less power need be generated and
distributed the same amount of useful energy to the
motor.
Just as the efficiency of an induction motor may be
reduced as its load decreases, the same is true for
the power factor only at a faster rate of decline.
A typical 10 HP, 1800 RPM, 3-phase, NEMA Design B
motor with a full load power factor of about 80 percent
decreases to about 65 percent as half-load. Therefore,
it is important not to oversize motors. Select the
right size motor for the right job.
- ● Demand Charges: The third
energy component affecting cost is demand charge and
is based on the peak or maximum power consumed or
demanded by an industrial customer during a specified
time interval. Because peak power demands may require
an electric utility to increase generating equipment
capacity, a penalty is assessed when demand exceeds
a certain level. This energy demand is measured by
a demand meter and a multiplier is applied to the
Real Power KW consumed. Cooling towers with varying
load requirements may be able to affect demand charges
by: 1) load cycling - stagger the starting and use
of all electrical equipment, and discontinue use during
peak power intervals, and 2) use of either electrical
or mechanical "soft start" hardware which
limits power in rush and permits a gradual increase
in power demand.
To be continued.
Please press the next button....
|