Valve positioner is a "closed loop" feedback
device which receives the control signal, (usually 3-15
psi) and supply pressure up to 100 psi, receives feedback
as to the blade position and adjusts the diaphragm pressure
to satisfy the control signal. Valve positioners are
used when air flow is critical. Control signals can
be "split-ranged" to actuate the fan control
using only 3-9 psi, or from 9-15 psi signal pressure.
The valve positioner receives
the control air signal and outputs a higher modulated
air pressure to the diaphragm which moves the fan blades
to their proper position to satisfy the air flow requirements
as called for by the temperature controller. For a 3
to 15 psi control signal the output pressure of the
valve positioner might be 7 to 23 psi to make the fan
blades moves to their required pitch angle. The advantage
of the valve positioner is precise air flow control
due to the feedback of blade pitch position and the
ability to output high pressure on the diaphragm to
quickly attain that position.
If air flow control is not
critical, an "open loop" system can be used.
The simplest would operate the fan using the 3-15 psi
signal alone. It is an "open loop" system
in that an air signal is imposed on the diaphragm and
the proper pitch angel is assumed to be attained. This
will be no problem for cooling towers that are not sensitive
to air flow and where 15 psi diaphragm pressure is sufficient
to move the blades through their required pitch travel.
Operation with only 3-15 psi is generally limited to
small fans.
An alternative device called
a bias relay can operate most fans in lieu of a valve
positioner. It is very simple, less expensive and requires
no maintenance. It is mounted in the "cold"
air outside the fan ring. A bias relay operates by receiving
the control signal, adding or subtracting a constant
pressure and multiplying the sum by a fixed gain. It
outputs a modulated higher pressure to simulate the
output of the valve positioner. The bias relay has to
be set for a particular fan application to provide diaphragm
pressure proportional to the instrument pressure to
make the blades move through their desired pitch travel.
Bias relays can provide the proper starting point so
the blades begin decreasing pitch at 3 psi, but with
a fixed multiplier or gain, they usually cannot provide
the output pressure to assure an exact 12 psi span.
Another point of interest
is hysteresis. There is a difference in the pitch angle
versus diaphragm pressure for increasing and decreasing
pressure. This is because of hysteresis in the hub operating
mechanism caused by friction. Hysteresis is practically
nil when a positioner is used and even if it is present
and there is a slight discrepancy in air flow to control
the cold water temperature, the temperature indicating
controller will merely output a signal correction to
meet the desired control point.
As an example, consider a
fan with 20o blade travel. This fan may require
a diaphragm pressure of 7 to 23 psi to get 20o
movement from the hub. A valve positioner can achieve
this exactly through its feedback mechanism. A bias
relay with a bias of + 0.5 psi and gain of 2 can achieve
the 7 psi diaphragm pressure with 3 psi input signal,
but at 15 psi signal its output is 31 psi. The 23 psi
diaphragm pressure is attained at a signal pressure
of only 11 psi giving a span of 3 - 11 psi instead of
3 - 15 psi. Below figure shows this difficulty. The
difficulty of obtaining an exact 12 psi instrument span
is caused by the lack of choices available for the fixed
multiplier (gain).
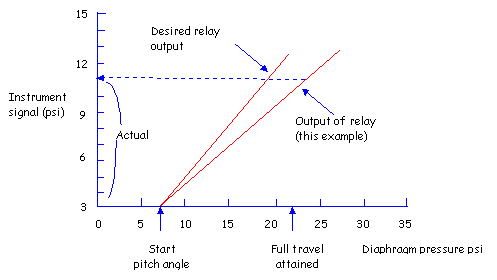
One of the most misunderstood
but important characteristics of the variable pitch
fan is the ability to "unload" or "feather"
for minimum power consumption automatically when the
ambient temperature decreases. The measurement of this
no-load power condition cannot be accurately determined
by the ratio method using voltage and amperage. Using
this method would lead one to believe the minimum power
consumption of a variable pitch fan in its feathered
position would still be 30 to 50 percent of the full
load. This is not true because three-phase power consumed
by the motor is calculated by the relation:
HPin = (Ampere)
x (Voltage) x 1.7321 x (Power Factor) / 0.746
Without measuring power factor,
accurate measurements cannot be made. Note, this would
be total power consumed at "no load" fan operation.
If we knew motor efficiency at no load we could calculate
HPout. No load power occurs at the "zero-flow"
position of the fan pitch, usually at about minus ten
degrees. This feathered mode occurs quite frequently
during daytime-nighttime and summer-winter ambient temperature
fluctuations and has importance in any power evaluation.
A typical case study to evaluate
the direct energy saving for variable pitch fans would
be prepared as follows; note that the same thermal conditions
were applied to this in order to compare the fan cost
differential between the fixed pitch fans and variable
pitch fans.
- ● 113-89.6-80.6
- ● 4 fans (14 feet)/cell
- ● Others remain unchanged
with the previous sample design excepting using the
fan ring instead of fan stack.
Below chart is to show how
the blade pitch shall be varied per the changes in the
airflow and air density, which results in the reduction
of heat load due to the change in the ambient wet-bulb
temperature. In estimating the energy comparison, the
following relation is a very simple approach but a useful
tool.
HP 2 = HP design
x (CFM 2/CFM design)2.8
x (Air Density 2/Air Density design)
Blade Pitch Chart (40HP
Motor) |
WBT
(oF/oC) |
80.6/27.0 |
78.8/26.0 |
77.0/25.0 |
75.2/24.0 |
73.4/23.0 |
71.6/22.0 |
Air
Flow (CFM) |
253096 |
232355 |
216053 |
202850 |
191824 |
182508 |
Static
Press. (" Aq.) |
0.464 |
0.394 |
0.342 |
0.302 |
0.271 |
0.246 |
Exit
WBT (oF/oC) |
102.06 |
102.54 |
102.94 |
103.29 |
103.59 |
103.86 |
Blade
Pitch |
13.3 |
10.5 |
8.7 |
7.1 |
5.8 |
4.8 |
Actual
Fan BHP (HP) |
31.9 |
24.2 |
19.4 |
16.1 |
13.6 |
11.6 |
HP
Saving |
0 |
24.1 |
39.2 |
49.5 |
57.4 |
63.6 |
Note: The air velocity at
the fill was significantly reduced at the 60.8oF
of ambient wet bulb temperature reaches in case of above
sample design. The normal range of air velocity in the
film fill is 300 to 700 fpm. If the air velocity is
less than the minimum 300 fpm at the fill, the fill
efficiency will be dramatically reduced since the air
shall not distributed to the entire fill evenly and
the air will not be smoothly upwarded due to the less
dynamic energy of air compared to the water loading.
In opposite case, that is,
if the air velocity is higher than the maximum 700 fpm
at the fill, all the fill efficiency shall be reduced
since the contacting time of air with water droplet
in the inside of fill is not enough to give the rated
mass heat transfer. To avoid this condition, the water
flow rate can be adjusted, some water may be bypassed,
or the some fans can be stopped.
Comparison
Table Between Two Speed Fan and Variable Pitch
Fan Control |
WBT
(oF/oC) |
80.6/27.0 |
78.8/26.0 |
77.0/25.0 |
75.2/24.0 |
73.4/23.0 |
71.6/22.0 |
Total
HP w/Adjustable Pitch Fan |
838.0 |
640.2 |
540.9 |
441.6 |
342.3 |
243.0 |
Total
HP W/Variable Pitch Fan |
765.6 |
580.8 |
465.6 |
386.4 |
326.4 |
278.4 |
Energy
Saving |
8.6 |
13.0 |
21.6 |
12.5 |
4.6 |
-14.6 |
Without full automatic control,
the human operator has very little incentive to be an
efficient and accurate power regulator in case of two
speed fan control. These have not proven very successful
for the most part for lack of control discipline. Accordingly,
the energy saving using variable pitch fan would be
far larger than above table.
|