2) International Applicable Standards of Noise
The noise phenomenon is not
easy to understand. According to physics it is the vibration
of air at frequency which can be heard by humans. The
vibration corresponds with very small air pressure variations.
Because the pressure variations cause noise which dissipates
energy, the noise will only persist if there is a source
which continuously generates the pressure variations.
The noise source is analogous to a light bulb shining
only while it is switched on. While the intensity of
a sound power generator cannot be measured directly,
the pressure variations are easy to measure at a specific
location, using a microphone. These are so called sound
pressure level (SPL) readings. The most common way to
determine the intensity or sound power level (PWL) of
the source is by calculation from several sound pressure
level measurements in the environment of the source.
Although it is difficult
to determine the sound power level of a noise source,
it is a more useful value to know than the pressure
level at a certain location. This is because the pressure
level can be predicted for every location only if the
power level is known.
The common way to express
sound pressure levels is in dimensionless logarithmic
relative ratios, or decibels. Rating the sound power
level of a source is done on the same way. One of the
advantages of the use of decibels is that it is possible
to define the relationship between sound power and sound
pressure levels very simply. Most of the national and
international measuring standards have been defined
within this scope.
One international standard
is known as ISO 3744. In the US there are several ANSI
and AMCA standards. All of these standards describes
a so called control area around a "black box"
which represents the noise source. In this control area
a certain number of readings have to be taken. Based
on the calculation of the average sound pressure level
from the measurements, the standards describe rather
simple methods to calculate the sound power level.
The one general noise specification
designed to protect "inplant" workers is the
Occupational Safety and Health Act of 1970, paragraph
1910.95. This criterion is based on sound pressure levels
in dB(A) and lists nine discreet pairs of sound levels
and associated permissible hours of duration. The sound
levels range from 90 dB(A) for 8 hours exposure to only
15 minutes allowable exposure to 115 dB(A).
Much more difficult criteria
have been established in Europe and some states, notably
California, which limits the total noise at the plant
boundary. In these cases the sound energy, or sound
power level of the total fan installation must be studied.
One of the most important factors in evaluating noise
is obtaining a precise definition of the point or locus
of points at which the noise specifications must be
met. It is not sufficient to state: "sound-pressure
levels must not exceed 90 dB(A)" without stating
where measurements will be taken.
The determination of the
sound performance of cooling fans is most often achieved
by using this method. The one complicating factor which
continuously arises is that a fan is not a "black
box" like a drilling machine or a motor. If measurements
are taken in the inlet or outlet air flow of the fan
they can be disturbed by the so called flow noise. To
prevent measuring interface from the air flow, the measurements
for a cooling fan have to be taken at a distance of
at least one fan diameter from the air inlet and outlet
of the cooling tower.
It is interesting to note
that the current CTI Code for Measurement of Sound From
Water-Cooling Towers limits itself to the sound pressure
measurement at a location which is agreed upon between
the client and supplier. Although this method had the
advantage of being very simple, it hardly contributes
to a more fundamental understanding of the noise problem.
Now, CTI is editing the current code as suggested by
DIN standard 45.635, part 46.
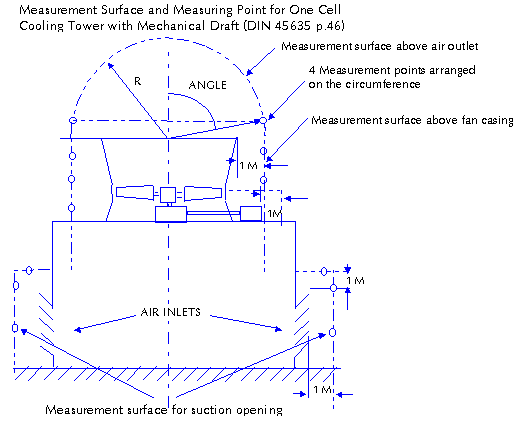
3) Sources of Noise in Cooling
Towers
The mechanical draft cooling
towers are a source of plant noise. Two principal sources
of mechanical draft tower noise are the fan and splashing
water. The splashing water noise contributes primarily
in the mid - to high frequency range, and the fan noise
contributes primarily in the low - to mid frequency
range. Therefore it is important to design each unit
to produce the minimum amount of noise while still meeting
the thermal requirements at a reasonable cost.
Noise in a cooling tower
is generated by the mechanical equipment; fan, motor,
gear reducer. Another source of noise in wet cooling
tower is a water falling (hitting) noise, which is generated
in hitting the water surface in the basin. Also the
noise generated by the water circulating pumps can not
be overlooked when they are installed outdoor at one
end of the cold water basin.
The water noise of major
five noise sources in an induced draft cooling tower
will prevail in near field conditions, which is located
within a distance of less than 4 to 5 times the air
inlet height in a counter flow configuration or 1 times
the air inlet height in a crossflow configuration. Beyond
that distance, the noise produced by the mechanical
equipment, mainly by the fan, will progressively become
predominant.
4) Fan Noise
In the cooling tower, the
fan is the sound power generator. The sound production
of a fan in operation consists of air borne sound and
contact sound. Since contact sound is related to tower
layout and orientation, etc., Hudson exclusively deal
with air borne sound only under the Hudson's test conditions.
Therefore actual environmental conditions do not consider
in sound power level calculated onto the fan rating
data sheet. The sound produced by fans consists of:
- ● Wideband noise caused
by vortex motion and turbulence in the flow.
- ● Pure tones plus harmonic
due to periodically alternating forces caused by the
Interaction of stationary parts and the moving blades.
Just measuring the noise
of a fan does not provide enough criteria to accurately
predict its noise performance. We must also know about
the influence of operating conditions and dimensions
on noise performance. Moreover, if noise production
must be reduced, an even more sophisticated understanding
of the noise generating mechanisms is necessary.
For a relatively slow running
fan, there are a few characteristic noise generating
flow phenomena. The so called "rotor self noise",
which is the turbulent and laminar vortex shedding at
the blade rear sections and at the blade tip. The ingestion
of turbulence in the main air flow. This turbulence
is generated by the fan supports or other upstream obstructions.
It leads to random variations in angles of incidence
at blade leading edges, causing fluctuating blade loads
and surface pressures over a broad range of frequencies.
Besides the broad band noise levels, sometimes there
are discrete peaks of sound pressure associated with
the blade passing frequency. This frequency is the product
of the fan rotation frequency and number of blades.
This noise is caused by the pressure pulsation which
is generated when a fan blade passes a sharp and close
disturbance such as a support beam. For a more simple
point of view, it can be stated that the noise intensity
of a cooling fan is related to the quantity and intensity
of flow generated swirls. Theoretically, all flow mechanism
as well as noise levels are controlled by the three
continuity laws of fluid dynamics; the continuity of
mass, impulse and energy. However, since these complex
equations cannot be solved for the flow situation in
a cooling tower, a more practical approach is required.
Unfortunately, in contrast with the measuring standards,
there is no internationally accepted method of performing
an analysis on cooling fan noise. There is no real agreement
between engineering societies on even the basic parameters
for calculating the expected fan noise for a particular
set of conditions. Some say noise is a function of tip
speed, static pressure, horsepower, flow, diameter,
or number of blades. Each maker has his own method.
The parameters we at Hudson feel most important are
tip speed and pressure differential across the fan.
Hudson's position is given in a paper by K.V. Shipes.
It is actually difficult
to calculate and guarantee the maximum noise level from
a fan in a new installation without having tested a
previous installation. Thousands of man-hours have been
invested in the study of fan noise in air-cooled heat
exchangers. These noise levels can be guaranteed on
full-scale tests. Field tests of standard cooling tower
modules must not be made to allow guaranteeing of cooling
tower fan noise. The effect of water noise further complicates
the problem.
When it is necessary for
tower/suppliers to furnish noise guarantees to customers,
it can be done if the fan manufacturer is given sufficient
data concerning the fan environment. If the measurement
is to be made at a point on grade level, a sketch is
helpful if it shows the orientation and dimensions of
the tower with respect to adjacent building or unusual
terrain. The height of fans above grade height of velocity-
recovery stacks, and exact location of the measurement
point or points is necessary.
Noise criteria should be
relayed to the manufacturer exactly as stated by the
specifications. Generally, OSHA requirements are not
difficult to meet if the concern is primarily fan-deck
noise. If a guaranteed noise level in a community several
miles away is required, the noise analysis becomes very
complicated because prevailing background noise and
attenuation of noise by the natural surroundings must
be considered.
Fan manufacturers must exempt
motor noise, gear reducer noise, and water noise from
any guarantee. They can be included for special cases
if sufficient data are given. Hudson is studying the
attenuation of sound-absorbing covers for the high-frequency
motor and gear reducer to help simplify this problem.
If any type of silencers are being considered for the
fans, check the economic. Most of Hudson's particular
fan noise is in the 125-500 hz bands. It may be cheaper
to slow the fan down, add more blades, and avoid the
silencer treatment. Each case must, of course, be considered
individually.
It is possible to decrease
fan noise about 10 dB by reducing tip speed from 12,000
fpm to 8,000 fpm. This reduction, however, would be
possible only if the fan being considered had the capability
of handling 125% more pressure and 50% more flow without
stalling.
To be continued. Please press the next button....
|