Because efficiency varies along pitch lines and with
air flow, power can be saved and noise & vibration
may be reduced by simply fine-tuning a fan? operating
point. At various speeds, calculate operating points
using speed factors, and check efficiencies at these
points on the fan curve. Speed factor = curve speed
/ actual speed. If, for example, the curve tip speed
was 12,000 ft/min, and the new speed is 10,000 ft/min,
the speed factor = 12,000/10,000 = 1.2. (This can also
be calculated in rpm. Tip speed = rpm x pie x fan diameter,
or rpm = tip speed / pie x D.)
After calculating the speed
factor, find the fan? new operating point: (ft3/min)2
= (ft3/min)1(speed factor), or
(total pressure)2 = (total pressure)1(speed
factor)2. Using the speed factor, the fan
speed can be changed at will. Each new speed and pitch
angle will improve or worsen the efficiency of original
starting point. Plot total pressure vs. ft/min air flow
for various pitch angles on the appropriate fan curve
to obtain the horsepower requirements. Note that the
pressure and flow work are the same at all the operating
points, at which pitch angles differ.
The point here is that, within
limits, the fan speed can be varied so that a pitch
angle can be selected which will optimize fan blade
efficiency and will satisfy the required system resistance.
Often it would be desirable to slow the fan down to
attain a higher, more efficient operating pitch angle
as an operating point. This also has a side benefit
of reducing noise and vibration because normally the
lower pitch angles which appear obvious choice to handle
the duty have lower efficiencies.
Still another aspect of system
efficiency is the proper selection of the fan diameter
for any given conditions, operating and economic. There
are several things which influence the choice of fan
diameter as below:
- ● Air Flow Range
- ● Fan Coverage
- ● Optimum Cell Size
- ● Evaluated Horsepower
- ● Standard Sizes Available
Of these, the most logical
influence is that the fan must provide the amount of
air flow required for any duty in a sensible operating
range. A quick look at any vendor's fan curve will yield
several sizes of fans to do any particular job. A poorly
sized fan will waste horsepower at the least and fail
to do the required duty at the worst.
For wet cooling towers, the
optimum cell size and evaluated horsepower comes into
play. Both are purely economic considerations. Optimum
cell size is obviously matching fan size to minimized
construction cost per cell. The evaluated horsepower
(E.H.) is increasingly becoming the major factor in
deciding fan diameters. E.H. is a "dollars per
horsepower" penalty added to a bid which is a measure
of operating costs of that design over the capitalized
life of that particular tower. Evaluated horse-power
of $550/hp to as much as $2,500/hp are becoming common.
The significance of E.H. is that very frequently the
difference in evaluated horsepower of several fan selections
can exceed the cost of the fan by many times.
In reviewing the potential
losses in efficiency in the fan itself we have discussed
two inherent losses that were built into the system
by design.
- ● Poor fan blade design
- ● Poor selection of operating
point
We also discussed the factor
of optimized diameter which was decided economically
before the air moving device was built. The two factors
which could be physically modified to reduce fan >system
losses would be the addition of the hub seal disc and
the revision of the fan operating point to a more efficient
condition, although a change in the number of blades
or gear reduction ratio might be required for the latter.
(2) The Fan Housing: The
components that make up the fan housing would be considered
a straight or velocity recovery stack for cooling towers.
The most important system loss for both types would
be the air leakage around the tips of fan blades. This
loss is a direct function of the tip clearance with
the stack and the velocity pressure at the operating
point. This leakage is caused by the tendency of the
high pressure exit air to recirculate around the tips
into the low pressure air in the inlet. The loss takes
the form of reducing the total efficiency and total
pressure capability of the fan. There are several areas
where inlet conditions can seriously affect the fan
system.
- ● Velocity Recovery Stack:
Refer to Chapter 4 for more details.
- ● Approach Velocity Consideration:
Sometimes the economics of structural costs may unintentionally
create very serious effects upon the system performance.
As with inlet losses to the fan, the magnitude of
the loss is a function of the velocity pressure which
itself is a function of air velocity. It is considered
good practice to insure that the air velocity at the
entrance to the fan is no more than approximately
one-half of the velocity through the fan throat.
(3) Unwanted Air Movements:
There are often cases where in order to increase performance,
you need to reduce air flow. These are cases where the
warm exit air flow recirculates to the inlet side of
the fan and decreases the mean temperature difference
between the cold entering air and the hot water temperature
in full thus lowering efficiency of the cooling tower.
The main factors which influence
the tendency to recirculate are primarily inlet or approach
velocity, exit velocity and velocity of prevailing winds.
Gunter and Ships have formulated simple analytical methods
to predict recirculation in a cooling tower utilizing
the above parameters. The primarily causes of recirculation
could be summarized as follows:
- ● Excessively high approach
velocities
- ● Units placed in line with
the prevailing wind direction
- ● Units placed at elevations
so that the exit of one is upstream of the inlet of
the adjacent unit.
- ● Low exit velocities, such
as those encountered in forced draft tower.
Severe performance problems
can result if recirculation is encountered. Recirculation
can be confirmed by smoke testing and by temperature
surveys of the exit and inlet air streams to a unit.
To eliminate recirculation it is usually necessary to
increase the exit airflow or changes the elevation of
the exit flow by adding straight sided fan stacks. In
some cases baffles may have to be considered.
In cooling towers the effect
of the velocity recovery stack is to reduce the exit
air velocity which could promote recirculation. It may
be necessary to utilize straight stacks to jet the hot
exit air further away from the approach or inlet areas.
Air leakage is another category
of unwanted air flow. Air leakage could occur in a cooling
tower at several places which lower the system efficiency.
- ● Missing access door panel
in the fan stack
- ● Holes (pass way of coupling
shaft) in the fan stacks
- ● Missing boards or holes
in the fan deck
The net result of these problems
is that the air movement intended to go through the
fill takes the path of least resistance and consumes
power but does not work.
3)Fan Tests
Since the fan test reports
are not available, the result of fan test applied to
the air cooled heat exchanger was quoted from a technical
paper published by Hudson. There will be no much difference
in the results with the application of cooling tower.
To illustrate the negative
effects on fan systems efficiency we have discussed,
a series of full scale fan tests were performed. The
basic scheme was to test a forced draft air cooler at
three different air flow rates in four conditions each:
- ● Standard (with inlet bell,
seal disc, and close tip clearance)
- ● Remove inlet bells only.
Test unit and replaces inlet bells.
- ● Remove seal disc only.
Test unit and replace seal disc.
- ● Increase blade tip clearance.
A total of twelve tests were
performed and a 20 feet x 32 feet, four row forced draft
air cooler with two 14 feet diameter fans was tested.
Modifications were made to the same single fan only.
The fan operated at 10,000 FPM tip speed and was equipped
with a 30 hp Reliance 1,160 rpm motor. The finned section
was a typical 1" O.D. - 10 fins per inch extruded
finned tube bundle. The unit was equipped with both
steam coils and louvers which were locked in an open
position during the test period. The testing equipment
used included the following:
- ● Taylor Model 3132 Anemometer
- ● Draft Gauge
- ● Tachometer
- ● Westinghouse Model PG-101
Power Analyzer
(1) Procedure: For each test,
air flow (CFM), static pressure, temperature, and electrical
power consumed was measured. Electrical measurements
included volts, amperes, watts, and power factor. Electrical
power input was calculated by the relation:
V x A x Power Factor x 31/2
HPoutput =----------------------------------------------
746
(Power factor: A measurement
of the time phase difference between the voltage and
current in an A-C circuit. It is represented by the
cosine of the angle of this phase difference. For an
angle of 0 degrees, the power factor is 100% and the
volt/amperes of the circuit are equal to the watts.
(This is the ideal and an unrealistic situation.) Power
factor is the ratio of Real Power-KW to total KVA or
the ratio of actual power (watts) to apparent power
(volt-amperes). Real Power-KW is the energy consumed
by the load. Real Power-KW is measured by a watthour
meter and is billed at a given rate ($/KW-HR). It is
the Real Power component that performs the useful work
and which is affected by motor efficiency.)
Velocity Pressure was calculated
by:
CFM
P = [--------------------------------------------- ]2
Inch Aq.
Net Free
Area of Fan x 4005
System Efficiency was calculated
by:
Total Pressure Actual x CFM
E = ---------------------------------------------
6356 x HPinput
Thus, the effect of only
one variable was investigated for each of three flows
which were at 0.061, 0.100 and 0.130 inches velocity
pressure.
(2) Discussion of Results:
Below table shows a comparison between curve fan efficiency
and the tested system efficiency. Test 1 and 2 showed
a 10 - 15 percent decrease from curve efficiency as
might be expected. Test 3 showed a 30 percent decrease
from curve efficiency which was surprising. Full scale
testing at best cannot achieve accuracy or repeatability
better than about plus or minus 5 percent. The effects
of ambient winds during the test period are by far the
biggest cause of error. Variations in velocity and direction
during the test period cause most problems while objects
around or on the test unit create eddy currents of wind
with corresponding high and low pressure areas. The
total system efficiency was considered "base"
performance for the tests >that followed.
Test |
Fan
Pitch |
Curve
Fan Efficiency |
Test
System Efficiency |
Test
1 |
14o
Pitch |
80.3% |
70.7% |
Test
2 |
8o
Pitch |
85.4% |
71.2% |
Test
3 |
3o
Pitch |
86.0% |
58.6% |
Considering the base performance
in each case was 100 percent, let us examine the effect
of each variable in turn. Below result of full scale
fan test curve shows the negative effect of only one
variable for each test point with the resulting decrease
in base system efficiency.
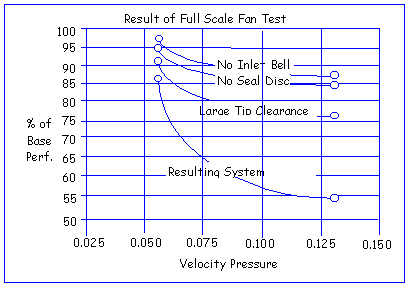
In reviewing the results
shown, it can easily be seen that the negative effects
that rob system efficiency are a function of the velocity
pressure. While not demonstrated on this test, previous
tests have shown also that the effects of the three
parameters studied are indeed cumulative. That is, the
total decrease in performance will be the sum of each
individual effect. Thus, we can see >that the negative
effects within the scope of this study would decrease
the base performance of this test fan by magnitudes
of 15 to an astonishing 58 percent. Keeping in mind
the previous decrease in "base" system performance
from the idealized "curve" system performance,
this should point out the importance of considering
the real system efficiency.
|