Fans can be driven by many different power sources such
as gas engines and turbines; however, the source most
frequently used is the electric motor. Like the fan
and system, which are equilibrium with each other throughout
their operating range, the fan and motor must also each
operate satisfactorily under all conditions. This chapter
outlines those items which must be considered when sizing
a motor to drive a fan.
1) Motor Capability
Motors are manufactured in
accordance with NEMA (National Electrical Manufacturers
Association) standards and are categorized by frame
size, type of enclosure, class of insulation, temperature
rise, voltage, speed, frequency etc. When operated within
the prescribed NEMA tolerances for voltage and frequency,
a motor will operate satisfactorily and maintain its
expected service life as long as the windings do not
over heat. Winding overheating causes premature insulation
failure and reduced motor service life. The winding
temperature is the sum of the ambient temperature, the
temperature rise due to the load on the motor, and a
hot spot allowance which is a function of the type of
enclosure selected. Some deviation from nameplate values
is possible as long as the windings do not overheat.
The motor service factor
is the ratio of power a motor can continuously produce
without reducing its service life, provided it is operated
at nameplate voltage and frequency, compared with its
nameplate horsepower. A service factor greater than
1.0 is primarily intended to provide a margin of safety
for variations in the operating parameters such as voltages,
frequency, line unbalance, sine wave shape, etc., and
is not intended to be used as a means of continuously
overloading the motor by purposely under sizing the
motor for the fan requirement. The operating conditions
of fans can be variously changed due to the change of
air density, air flow, etc. excepting the operating
variations in the electric power sources. So, 1.15 service
factor is quite required to the cooling tower application.
2) Aerodynamic Considerations
A fan's output and power
requirement have a direct linear relationship to the
density of air entering the fan inlet. If the air density
drops, then the fan's output and power requirement also
drop. The reverse is also true. Motors can overload
when the air density increases, such as in cold weather.
The power required versus the power available from the
motor should be evaluated for the entire anticipated
range of operation. Fans at operating conditions may
require special caution during cold start-up conditions
so as to not seriously over-load the motor.
Design margins that may be
included in the initial system resistance calculations
can cause the fan to operate at another location on
the fan curve than the intended design point. Depending
upon the slope and shape of the fan curve, the power
required may be larger than expected and the motor could
overload if not enough margin was left between the fan
power required and the motor capability.
Fan ratings are based on
tests conducted in a laboratory using AMCA Standard
210. This standard specifies test setup configurations
so that accurate and repeatable test results are obtained.
When a fan is installed in the field, the inlet or outlet
connections can cause distorted velocity profiles which
alter the expected fan performance. Test programs have
demonstrated that depending upon the severity of the
distortion and whether there is swirl in the air stream
opposite to the direction of impeller rotation, fan
power requirements may be larger than expected.
3) Mechanical Consideration
Several mechanical considerations
involving physical aspects of a fan application must
be evaluated when sizing a motor. Some of the most common
ones are described as follows.
(1) Drive Train Losses: AMCA
Standard 210 defines fan power input as the power required
to drive the fan and any element (gear reducer &
coupling shaft) in the drive train that is considered
part of the fan. We don't need to consider the loss
in the power for the shaft, but the loss for the gear
reducer should be included in the evaluation of the
fan shaft power.
(2) Motor Slip: Ship is a
term which describes the percentage of difference between
the synchronous speed and the actual speed of motor
under load. Slip generally increases with an increase
in motor torque; therefore, actual operating speed generally
decreases with an increase in motor torque. Specify
this full load speed when sizing the fans. If slip is
not considered, the fan may not run at the selected
speed.
Synchronous Speed of Motor
= 120 x Frequency / Number of Pole (RPM)
Where,
120 = AC current flow changes 120 times every second.
(2 RPM/Cycle)
Number of Pole: always pairs (couple of S-pole and N-pole)
in the pole of motor. The rotation of motor shaft will
occur because of the magnetic phenomenon that unlike
magnetic poles attract each other and like poles repel.
If we progressively change the polarity of the stator
poles in such away that their combined magnetic filed
rotates, then the rotor will follow and rotate with
the magnetic field of the stator. Accordingly, the speed
of the rotating magnetic field set up by the stator
winding of an induction motor. In a synchronous motor
the rotor locks into step with the rotating magnetic
field, and the motor is said to run at synchronous speed.
Pair pole rolls to restrict the motor speed.
Percent Motor Slip = Synchronous
Speed - Full Load Speed / Synchronous Speed x 100 (%)
The smaller % motor slip
is the higher power rating. The % motor slip of energy
efficient motor is smaller then one of standard efficient
motor.
(3) Motor Bearing Life: Specify
a motor bearing life consistent with the specified gear
reducer bearing life. Motor manufacturer can supply
bearing lives when given the appropriate information.
(Speed torque curve of load and Inertia moment of load,
etc.)
(4) Torque: The full load
torque is expressed as 5250 x Hp / Full Load Speed (lbs-ft).
Since different loads present different torque requirement
at starting (= breakaway), minimum (= pull up), breakdown
(= pull-out) and full load, NEMA has defined four standard
design classes A, B, C and D of squirrel cage poly-phase
induction motors. These design classes are summarized
in below table.
NEMA
Design |
Starting
Torque |
Starting
Current |
Breakdown
Torque |
Full
Load Slip |
A |
Normal |
High |
High |
Low |
B |
Normal |
Normal |
Normal |
Normal |
C |
High |
Normal |
Normal |
Normal |
D |
Very
High |
Low |
- |
High |
NEMA Design "B"
of above is a standard general-purpose design. This
has low starting current, normal torque, and normal
slip. The field of application is very broad and includes
fans, blowers, pumps, and machine tools. This design
is a best choice as a driver of cooling tower fan.
The general torque/speed
relationship with the four torque points defined is
shown in below figure.
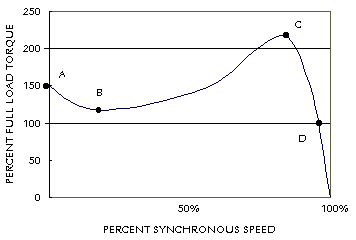
- A. Breakaway or Starting
Torque: This torque is normally defined by motor manufacturers
as "locked-rotor" torque. It is the torque
required to start a shaft turning. Methods of bearing
lubrication and types of lubricants have a pronounced
effect on this torque requirement. Some loads just
harder to start turning than others. (In most NEMA
Design B and one winding motors, this torque is equal
to 160 to 180% to the full load torque.)
- B. Minimum or Pull-Up Torque:
This torque, usually expressed in percent of running
torque, is required to accelerate the load from standstill
to full speed. It is the torque required not only
to overcome friction, windage, and product loading
but also to overcome the inertia of the machine. The
torque required by a machine may not be constant after
the machine has started to turn. This type of load
is particularly characteristic of fans and centrifugal
pumps.
In considering the torque required by a machine during
acceleration, its maximum torque required is the most
significant. The minimum accelerating torque capability
of the driving motor must exceed the maximum accelerating
torque required by the machine. Special consideration
must be given to the selection of the motor to assure
that it will have the necessary thermal capacity to
bring the machine to full speed. During the period
of acceleration one-half of the energy input to the
motor is absorbed by the motor rotor circuit while
the other half is stored in the driven machine. In
larger cage motors of conventional design the temperature
rise of the rotor may limit its ability to accelerate
a high-inertia load to its full speed. (In most NEMA
Design B and one winding motors, this torque is equivalent
to 150 to 170% to the full load torque.)
- C. Breakdown or Pull-Out
Torque: This torque is generally called peak torque
or maximum torque. The peak torque is the maximum
momentary torque that a machine may require from its
driving motor. The peak torque required by a load
is directly related to the "breakdown" or
"pull-out" torque for its driving motor.
High peak torque requirements for brief periods of
time are available from the break-down torque of an
induction motor assisted by the inertia of the rotating
system. If the peak-torque requirement is of any appreciable
duration, however, it is necessary that the breakdown
torque exceed the peak-load requirement. The term
"pull-out" torque usually refers to the
maximum running torque of a synchronous motor. Inertial
energy cannot assist the pull-out torque in carrying
a peak-torque requirement of the load unless the motor
is of the non salient-pole or the reluctance type.
It is therefore necessary in practically every instance
to consider specifying a synchronous motor whose breakdown
or pull-out torque exceeds the peak running torque
of the load. (In most NEMA Design B and one winding
motors, this torque is equivalent to 250 to 350% to
the full load torque.)
- D. Full Load Torque: This
torque is a normal and continuous torque produced
by motor at the full load speed.
To be continued.
Please press the next button....
|