1) General
When a body or system is
given with an initial displacement from its equilibrium
position and is released, it will vibrate with a definite
frequency called as the natural frequency. In other
word, if you were to suspend a slender article and you
begin vibrating it at varying frequencies, beginning
at zero hz or at some point it would begin to vibrate
dramatically as its resonant frequency (RF) was reached.
This is a point where its natural frequency to vibrate
was exited by an equal applied source and it would resonate.
This is a characteristic
of any mass but we are discussing fan blades of any
size or type. Additionally, the resonant frequency of
an operating fan will be somewhat higher than the measured
static natural frequency because of the stiffening effect
of centrifugal force. Hudson provides first and second
modes of blade natural frequencies. These first mode
& second mode resonant frequencies were actually
measured on a special vibration mount by a real time
analyzer for recording and obtaining them.
2) Fan Dynamic Characteristics
Cooling tower fans for the
electric utility and petrochemical process industries
are used in sizes varying from 12 ft to 60 ft in diameter
of cooling tower, with common fan sizes in the 26-30
ft range. Because fan efficiency has become a significant
factor in evaluating cooling tower costs, the larger,
more efficient fans are usually selected in new applications,
often without sufficient regard to such an important
factor as fan dynamic response at low speeds.
Also, the fan's low operating
speeds require special and often unfamiliar equipment
for analysis and monitoring. Adherence to a few basic
rules during fan selection can greatly reduce this dynamic
response and associated fan stresses. Implementation
of a regular maintenance program based on vibration
trend analysis is also imperative to enable scheduling
of preventive maintenance and balancing activities.
If a failure is imminent, electronic monitoring devices
that respond over an extended frequency spectrum can
give warning before severe damages is done to the tower
or the fan.
To ensure the optimum operating
condition of cooling tower fans there are several important
things for operating frequencies and resonant frequency
margin which have to be carefully considered. Investigation
into the dynamic response of a fan blade begins with
the determination of the static natural frequency (fs)of
the blade. This value can be easily determined for the
first mode of vibration by striking the blade and then
recording this frequency with a vibration meter. To
correct for the effects of centrifugal forces at fan
operating speed, this static natural frequency must
be converted to dynamic natural frequency (fd).
This is done by using the following equation; fd
= {(fs)2 + K x RPM}1/2,
where fs and fd are both expressed
in cycles/min. and K is a constant, whose value is 1.5
for most fans.
For most large diameter cooling
tower fans the first mode dynamic natural blade frequency
is usually much higher than the allowable operational
speed of the fan. Limits on fan speed are governed by
blade stress and fan noise. This limit is generally
considered to be the speed at which blade tip velocity
is 12,000 ft/min. Thus, it is rare to find a cooling
tower fan speed that is coincident with its blades'
first dynamic natural frequency.
There are two fan operating
frequencies which should be separated from the natural
frequency of blade in order to avoid resonance at fan.
If the force or displacement is applied with a frequency
close to the natural frequency of the system, the amplitude
of vibration in a system becomes extremely large. This
force or displacement is resonance.
As you can see from the definition
of the resonance, the vibration amplitude becomes very
large as a typical symptom. It is often misunderstood
as a fan unbalance problem if there is no vibration
analysis capability. However, the resonance problem
is a far more dangerous and complex, and the cure can
be very expensive requiring either change the motor
speed or add blade number.
(1) Typical Natural Frequency
Spectrum: The peak of natural frequencies on blades
are very narrow (2 or 3 hz) due to the fiberglass composite
structure requiring less separation than the metal (Aluminum)
construction blades. Typical natural frequency spectrum
normally follows a signature as below.
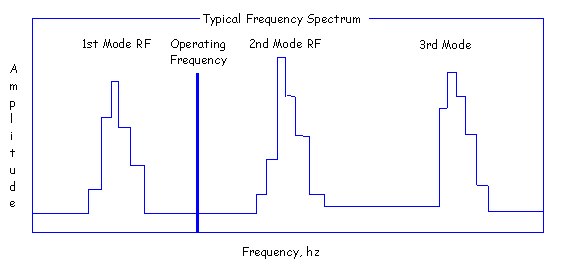
As the operating frequency
gets close to the center of natural frequency mode,
the dynamic stiffness of asystem rapidly decrease compare
to the static structural stiffness. This causes the
high vibration amplitude. Considering the peak profile
characteristics of natural frequency modes and the past
experiences, we feel that the minimum separation of
10% away from any natural frequencies is desirable.
(2) Fan Operating Frequencies
(a) Blade Pass Frequency
(BPF): Vibrations that are significant to the cooling
tower structure are those thatare induced as multiples
of the fan operational speed. These impulse forces or
excitation frequencies are functions of the number and
order of location of the supporting structures underlying
the fan. The basic structural excitation frequency is
commonly referred to as the blade pass frequency (BPF)
and is calculated by this equation:
BPF = No. of Blades x
Fan rpm / 60 (hz)
This is the frequency where
the blades aerodynamically excites the supporting beam
or tower structure. If a resonance occurs at this frequency,
large vibration will be exhibited at the tower structure.
The natural frequency of your tower structures should
be away from this frequency. This can be a great destruction
of fan blades when the blade passing frequency equals
the resonant frequency.
The frequency of blade vibration
may differ from the BPF if large beams, drive shaft
or other obstructions are within about 2 feet from blades.
In this case BPF shall be modified by "N"
times obstruction. Such as two beams close to the tops
may cause a frequency of (2 x BPF) hz. This frequency
would have to be compared to the blade's resonant frequency
of an exciting force is in harmony with the fan dynamic
frequency. Aerodynamic forces generated by blades passing
over structural members, lubrication lines, drive shafts,
etc. will excite blade vibration at a frequency determined
by the number of times per revolution blades pass over
obstructions. These critical speed occurs at 2, 3, 4...N
cycles per revolution frequency depending on the number
of obstructions.
Best results will be obtained
if this basic excitation frequency is kept at least
three times as high as the fan blade natural dynamic
frequency. Equally importance is the associated components
of the cooling tower, such as drivelines, fan stacks,
beams, etc. which must be tuned to avoid resonance with
this basic BPF.
Problems encountered with
BPF resonance are usually destructive, and merit immediate
attention. One solution is to change the natural frequency
response of the components or blades, another is to
change the BPF. Changing the BPF can be done by varying
either the fan speed or the blade number. Because the
later solution involves considerable expense in fan
or gear change out, the more practical solution is usually
to tune and damp the tower structure by bracing or weighting
the individual components. This will help control vibrations
induced by the fan relative to the structure.
While necessary to prevent
structural problems, measurement of vibration levels
on the cooling tower structures tells little about the
fan blade itself and its position in the air it is moving.
For this reason, wave front analysis techniques have
been developed that use telemetry systems to provide
stress and acceleration data from the blades as they
transit the throat of the fan stack. Frequency spectrum
or signature analysis of these data has consistently
revealed that these fans experience impulses at all
fundamental harmonics of the operating speed.
These excitation forces are
created by wave front in the air flow due to the structural
patterns found in the plenum directly below the fan.
Structural obstructions include wood, concrete, or steel
beams, piping conduit, and wind walls.
The effect obstructions have
on the air flow is to create dead spots or wave fronts
where the air direction is changed or is turbulent.
These wave front occur in mathematical series similar
to the geometric patterns of the obstructions creating
them. As a fan blade makes a revolution, it encounters
air loading impulses - excitation forces - in a periodic
function that can constitute integral multiples of the
operating speed. Therefore, the fan blade's natural
dynamic frequency (fd) must not coincide
with any multiple of fan rpm.
When selecting fan operational
speed it is also important to consider the expected
variance in the dynamic natural frequency from blade
to blade. If, for example, 28 ft diameter blade's natural
frequency were to vary +/- 4%, the possibility of encountering
a critical frequency situation is significant. Note
that the excitation frequency responses at integral
multiples of fan rpm can greatly restrict the speeds
at which the blade can operate given the variance in
its natural dynamic frequency.
Good engineering practice
dictates that these potential driving forces at integral
multiples of rpm be kept at a critical range of at least
10% away from the natural frequencies of the fan blades,
to avoid resonant amplifications of forces. Because
the fan must avoid all multiples of fan rpm, the critical
range should be calculated for (N = 1, 2, 3, ...) using
this equation: CR = (N x RPM - fd) / rpm
x 100.
Due to these dynamic characteristics,
large diameter cooling tower fans are not suitable for
variable speed service. Programs that attempt to conserve
energy by proposing that fans be driven at variable
speeds run the risk of encountering severe vibration
problems. In such an installation, the cooling tower's
plenum chamber would have to be relatively free of flow
disruptive structures. Fan blades with high damping
factors would also be required, to resist the amplification
of forces.
If conservation of fan energy
is required, the best approach is use of a two speed
electric motor. This will provide no problem, because
fans that are operating at full speed in safe critical
frequency ranges will automatically be in the same ranges
at half speed. Variable pitch fans are also an acceptable
method of controlling fan flow and energy, and this
is the method that is recommended in cases where a precise
level of fan throttling is needed.
(b) Beam Pass Frequency:
This is the frequency where the aerodynamic effect of
the beam occurs to fan blade and is obtained from an
equation of Beam Pass Frequency = No. of Beam x Fan
rpm / 60 (hz). If a resonance occurs at this frequency,
the blade might be damaged at its mode(s) depending
on the mode type (i.e. first or second mode) where the
excitement force coincides at. In normal cases, this
frequency is less important since the RF margin exceed
the minimum 5%, but there is often a case to carefully
consider the RF margin in case of small number of fan
blades.
To be continued. Please press the next button....
|